Gas travel distance& efficiency
-
- Private 2
- Posts: 23
- Joined: Wed Sep 16, 2015 3:31 am
As you can see there are 2 cannon in my attachment. One has longer distance between air tank and barrel and the other is shorter. Which one is more efficiency? Both of them have same size air tank and barrel but longer pipe between them. Will the velocity of the bullet be affected greatly or little or none?
- jackssmirkingrevenge
- Five Star General
- Posts: 26183
- Joined: Thu Mar 15, 2007 11:28 pm
- Has thanked: 547 times
- Been thanked: 326 times
The second one is less efficient. The air has more place to expand before it reaches the projectile (what we call "more dead volume"), meaning that you will have less barrel pressure and therefore less velocity for the same chamber volume and barrel length.
hectmarr wrote:You have to make many weapons, because this field is long and short life
Does this cause co-axial builds to be less efficient as well?jackssmirkingrevenge wrote:The second one is less efficient. The air has more place to expand before it reaches the projectile (what we call "more dead volume"), meaning that you will have less barrel pressure and therefore less velocity for the same chamber volume and barrel length.
-
- Private 2
- Posts: 23
- Joined: Wed Sep 16, 2015 3:31 am
Thank you! I will try to reduce the "dead volume" in my designjackssmirkingrevenge wrote:The second one is less efficient. The air has more place to expand before it reaches the projectile (what we call "more dead volume"), meaning that you will have less barrel pressure and therefore less velocity for the same chamber volume and barrel length.
- jackssmirkingrevenge
- Five Star General
- Posts: 26183
- Joined: Thu Mar 15, 2007 11:28 pm
- Has thanked: 547 times
- Been thanked: 326 times
Coaxials don't have this problem, though they are in theory less efficient because the air has to do a 180 degree turn to leave the barrel. In practice this difference compared to an inline valve is hardly measurable though.vng21092 wrote:Does this cause co-axial builds to be less efficient as well?
hectmarr wrote:You have to make many weapons, because this field is long and short life
-
- Private 2
- Posts: 23
- Joined: Wed Sep 16, 2015 3:31 am
What does Coaxials means? does it means that the air bends between reaching the barrel?
- Fnord
- First Sergeant 2
- Posts: 2239
- Joined: Tue Feb 13, 2007 9:20 pm
- Location: Pripyat
- Been thanked: 1 time
- Contact:
The second is less efficient but there may be exceptions to this rule.
Because the gas accelerates to a significant velocity before it encounters the projectile, it will experience shock heating from the sudden recompression. With the right type of projectile, valve and barrel you can see some noticeable velocity gains.
If you've made the gun from metal it may also be possible to lightly coat the projectile in a volatile hydrocarbon and get a dieseling effect upon firing.
I'm sure Ragnarok will come along shortly and spew maths onto the page in a more comprehensive explanation.
Because the gas accelerates to a significant velocity before it encounters the projectile, it will experience shock heating from the sudden recompression. With the right type of projectile, valve and barrel you can see some noticeable velocity gains.
If you've made the gun from metal it may also be possible to lightly coat the projectile in a volatile hydrocarbon and get a dieseling effect upon firing.
I'm sure Ragnarok will come along shortly and spew maths onto the page in a more comprehensive explanation.
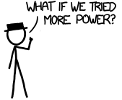
And here is a Ragnarok, but not with that much maths.
Firstly, you have got the shock or adiabatic heating effects which Fnord mentioned - the heat reduces the density of the propellant gas (for a given pressure) and thus potentially improves efficiency at higher velocities (which is why light gas guns use light gases).
I've experimented on some level with adiabatic effects, where I had a "plunger" in the barrel that separated the air coming from the valve from an artificial dead volume I'd made by deliberately starting with the projectile and its sabot about half way along the barrel - the intention being that this air between the plunger and sabot would get ludicrously hot when it was rapidly compressed and thus be able to accelerate the projectile to velocities impractical with standard temperature air.
The results were fairly promising, pushing .177 pellets past even the most ludicrous airgun velocity claims (and I was doing it with full weight lead pellets, not light weight alloy ones), although probably interesting only as an experiment, as there are lots of more practical ways to achieve the same results (like using helium or swapping to a low-mix hybrid).
Another possible effect is something similar to an electrical capacitor - while the dead volume absorbs some of the energy in the system, it also has less restricted flow than the main valve.
It depends on the dynamics of the specific launcher and projectile, but if the launcher's velocity is sufficiently high as compared to the valve flow rate, then the volume stores some air when the valve is first opened (and the projectile is barely moving), which it can put back into the barrel when the projectile is reaching the far end of the barrel (and the space behind said projectile is growing faster than the valve can fill it from the chamber).
For an example, a quick simulation shows that HEAL with no dead volume would launch an 8 gram dart at 262 m/s. Modelling it with its actual ~40cc dead volume, the velocity increases slightly to 266 m/s.
And that's with a pretty powerful valve - if I halve the modelled valve flow, it's a larger jump from 219 m/s up to 227 m/s.
However, in all fairness, keeping dead volume to a practicable minimum is hardly a bad rule of thumb - the effects involved are usually limited and hard to optimise (needing accurate valve specifications).
But it does mean I wouldn't get too worried about eliminating every last cubic millimetre of dead volume*, as it's very often not as bad as some people think.
*For me, I've designed my last few pneumatic launchers with a ball valve between the main piston valve and the breech. Some people have commented about the added dead volume, but any such difference is nearly irrelevant and having a dependable safety is far more significant to me.
Firstly, you have got the shock or adiabatic heating effects which Fnord mentioned - the heat reduces the density of the propellant gas (for a given pressure) and thus potentially improves efficiency at higher velocities (which is why light gas guns use light gases).
I've experimented on some level with adiabatic effects, where I had a "plunger" in the barrel that separated the air coming from the valve from an artificial dead volume I'd made by deliberately starting with the projectile and its sabot about half way along the barrel - the intention being that this air between the plunger and sabot would get ludicrously hot when it was rapidly compressed and thus be able to accelerate the projectile to velocities impractical with standard temperature air.
The results were fairly promising, pushing .177 pellets past even the most ludicrous airgun velocity claims (and I was doing it with full weight lead pellets, not light weight alloy ones), although probably interesting only as an experiment, as there are lots of more practical ways to achieve the same results (like using helium or swapping to a low-mix hybrid).
Another possible effect is something similar to an electrical capacitor - while the dead volume absorbs some of the energy in the system, it also has less restricted flow than the main valve.
It depends on the dynamics of the specific launcher and projectile, but if the launcher's velocity is sufficiently high as compared to the valve flow rate, then the volume stores some air when the valve is first opened (and the projectile is barely moving), which it can put back into the barrel when the projectile is reaching the far end of the barrel (and the space behind said projectile is growing faster than the valve can fill it from the chamber).
For an example, a quick simulation shows that HEAL with no dead volume would launch an 8 gram dart at 262 m/s. Modelling it with its actual ~40cc dead volume, the velocity increases slightly to 266 m/s.
And that's with a pretty powerful valve - if I halve the modelled valve flow, it's a larger jump from 219 m/s up to 227 m/s.
However, in all fairness, keeping dead volume to a practicable minimum is hardly a bad rule of thumb - the effects involved are usually limited and hard to optimise (needing accurate valve specifications).
But it does mean I wouldn't get too worried about eliminating every last cubic millimetre of dead volume*, as it's very often not as bad as some people think.
*For me, I've designed my last few pneumatic launchers with a ball valve between the main piston valve and the breech. Some people have commented about the added dead volume, but any such difference is nearly irrelevant and having a dependable safety is far more significant to me.
Does that thing kinda look like a big cat to you?
-
- Private 2
- Posts: 23
- Joined: Wed Sep 16, 2015 3:31 am
Thank you , well explained. No more question
- jackssmirkingrevenge
- Five Star General
- Posts: 26183
- Joined: Thu Mar 15, 2007 11:28 pm
- Has thanked: 547 times
- Been thanked: 326 times
There was much talk of this but I didn't mention it as it tends to be outside the realm of most spudding projects.The second is less efficient but there may be exceptions to this rule.
There are ways to have it inline, like a burst disk for example:But in essence, don't they all make a 180? I mean

hectmarr wrote:You have to make many weapons, because this field is long and short life