Homemade piezoelectric pressure transducer
I've designed a circuit to correctly measure pressure as a function of time and tell you when the projectile leaves the barrel and it's muzzle velocity with a little analysis of the signal. Typical piezoelectric pressure transducers I've seen usually cost $100 or more, so a DIY option designed specifically for spudding is highly desirable to the more theoretical crowd.
I say "correctly measure pressure as a function of time" because the piezo transducer circuits I've seen are made wrong and their output is not interpreted correctly. jimmy's old circuit was a good start but gets a number of things wrong, namely...
- The voltage across a piezoelectric element is proportional to the pressure differential, not the derivative of the pressure with respect to time. The wacky fluctuations seen in jimmy's circuit are likely due to a combination of sound, #2, and #3.
- The piezoelectric element's capacitance makes it act like a high pass filter. This means that "slow" pressure changes (i.e. on the order of a millisecond) don't register unless you design the circuit to compensate for this. In practice this means a high capacitance piezoelectric element and a high resistance potentiometer are necessary to increase the RC time constant.
- The measurement is likely affected by loading from the PC microphone input. A buffer is necessary. An op. amp can do this.
- You can't tell precisely when the projectile has left the barrel. A phototransistor will do this. Two phototransistors will make a dual purpose circuit that will also tell you the muzzle velocity.
- The circuit can compensate for the filtering the computer does (at least if the mic. input circuits are similar to the ones I've seen online which are simple high-pass filters). Two op. amps can do this.
A quick and not completely accurate drawing of the my current planned circuit is here: http://trettel.org/images/pressure%20tr ... 0309_1.jpg
The top circuit is the pressure transducer itself with the phototransistors. A comparator switches the signal from the pressure curve to a higher voltage when the projectile passes over a phototransistor.
The middle circuit is simply two batteries (and it's supposed to have a SPDT switch).
The bottom circuit compensates for the filtering I believe the computer microphone input does. I assume the computer microphone input is similar to the simple high pass filters I saw when researching it. The variable capacitor is adjusted until the input signal is unaffected. The circuit itself simply is an inverting amplifier with a capacitor in series with the feedback resistor and a second inverting amplifier with no gain. The total gain of this circuit as a function of frequency is the inverse of a simple high pass filter.
I have enough components to make a test circuit over the next few days, but... I'm not an electrical engineer and my knowledge of electronics does not go far beyond what is taught in the electrical courses for undergraduate mechanical engineers. Maybe someone here with more electronics knowledge could have some suggestions or even tell me that I'm doing it completely wrong (and if I am, please say so).
I say "correctly measure pressure as a function of time" because the piezo transducer circuits I've seen are made wrong and their output is not interpreted correctly. jimmy's old circuit was a good start but gets a number of things wrong, namely...
- The voltage across a piezoelectric element is proportional to the pressure differential, not the derivative of the pressure with respect to time. The wacky fluctuations seen in jimmy's circuit are likely due to a combination of sound, #2, and #3.
- The piezoelectric element's capacitance makes it act like a high pass filter. This means that "slow" pressure changes (i.e. on the order of a millisecond) don't register unless you design the circuit to compensate for this. In practice this means a high capacitance piezoelectric element and a high resistance potentiometer are necessary to increase the RC time constant.
- The measurement is likely affected by loading from the PC microphone input. A buffer is necessary. An op. amp can do this.
- You can't tell precisely when the projectile has left the barrel. A phototransistor will do this. Two phototransistors will make a dual purpose circuit that will also tell you the muzzle velocity.
- The circuit can compensate for the filtering the computer does (at least if the mic. input circuits are similar to the ones I've seen online which are simple high-pass filters). Two op. amps can do this.
A quick and not completely accurate drawing of the my current planned circuit is here: http://trettel.org/images/pressure%20tr ... 0309_1.jpg
The top circuit is the pressure transducer itself with the phototransistors. A comparator switches the signal from the pressure curve to a higher voltage when the projectile passes over a phototransistor.
The middle circuit is simply two batteries (and it's supposed to have a SPDT switch).
The bottom circuit compensates for the filtering I believe the computer microphone input does. I assume the computer microphone input is similar to the simple high pass filters I saw when researching it. The variable capacitor is adjusted until the input signal is unaffected. The circuit itself simply is an inverting amplifier with a capacitor in series with the feedback resistor and a second inverting amplifier with no gain. The total gain of this circuit as a function of frequency is the inverse of a simple high pass filter.
I have enough components to make a test circuit over the next few days, but... I'm not an electrical engineer and my knowledge of electronics does not go far beyond what is taught in the electrical courses for undergraduate mechanical engineers. Maybe someone here with more electronics knowledge could have some suggestions or even tell me that I'm doing it completely wrong (and if I am, please say so).
All spud gun related projects are currently on hold.
-
- Corporal 5
- Posts: 986
- Joined: Thu Jun 16, 2005 1:44 pm
- Been thanked: 1 time
Uhhh...I'm no expert, but I think that filter may saturate on you:
Since:
Av=Rf/R
With a DC signal, the cap will force Rf to be an open, so therefore you now have:
Av= Infinity/R
Now you are using an AC input, but there are small offset voltages on an Op-Amp, which when amplified by infinity, may cause some problems
Most of the active low-pass inverting filter designs I've seen put the cap in parallel with the resistor. This would bypass the above issue, since there would still be a resistor to keep the gain in check.
I could be wrong, just thought I should point it out.
Since:
Av=Rf/R
With a DC signal, the cap will force Rf to be an open, so therefore you now have:
Av= Infinity/R
Now you are using an AC input, but there are small offset voltages on an Op-Amp, which when amplified by infinity, may cause some problems

Most of the active low-pass inverting filter designs I've seen put the cap in parallel with the resistor. This would bypass the above issue, since there would still be a resistor to keep the gain in check.
I could be wrong, just thought I should point it out.
"If at first you dont succeed, then skydiving is not for you" - Darwin Awards
I had thought of that, yes, but not including the offset voltages. I can't put the capacitor in parallel with the resistor because the gain wouldn't be right (as I said, the gain of the filter is the inverse of the gain of the microphone input). I can however put a big resistor in parallel to prevent saturation. The op-amps I plan to use all say they have low offset voltages so I didn't think it'll be a problem, but I also admittedly know nothing about electronics. Thanks for bringing this up.
Learning something about Fourier analysis would probably also help a good deal to determine precisely what'll happen, but I'm busy enough.
Learning something about Fourier analysis would probably also help a good deal to determine precisely what'll happen, but I'm busy enough.
All spud gun related projects are currently on hold.
-
- Corporal 5
- Posts: 986
- Joined: Thu Jun 16, 2005 1:44 pm
- Been thanked: 1 time
Can't you just use that second amplifier cascaded with the filter to adjust the gain as need be?
"If at first you dont succeed, then skydiving is not for you" - Darwin Awards
I'm confused as to why I'd do that. Perhaps I'm using the wrong terminology. I'll explain what I'm doing in a little more detail.
The transfer function for the microphone input is H(jω) = R / (Zc + R) where R is a resistance and Zc is the complex impedance of the capacitor. I need to make a filter/amplifier than is the inverse of this, so H(jω) = (Zc + R) / R (when these two transfer functions/gains are multiplied together they cancel out). The combination of two op. amps does that. The first one has a transfer function of -(Zc + R) / R and the second one inverts that signal.
The transfer function for the microphone input is H(jω) = R / (Zc + R) where R is a resistance and Zc is the complex impedance of the capacitor. I need to make a filter/amplifier than is the inverse of this, so H(jω) = (Zc + R) / R (when these two transfer functions/gains are multiplied together they cancel out). The combination of two op. amps does that. The first one has a transfer function of -(Zc + R) / R and the second one inverts that signal.
All spud gun related projects are currently on hold.
-
- Corporal 5
- Posts: 986
- Joined: Thu Jun 16, 2005 1:44 pm
- Been thanked: 1 time
Oh, I think I get it now. I still think it might be a better idea to seperate your amplification from your filtering (well, I guess you aren't really "filtering"). The sound card will also probably have a better filter than a simple RC circuit.
May as well just try it as-is, worse comes to worse you move a capacitor
May as well just try it as-is, worse comes to worse you move a capacitor

"If at first you dont succeed, then skydiving is not for you" - Darwin Awards
- Technician1002
- Captain
- Posts: 5189
- Joined: Sat Apr 04, 2009 11:10 am
I have a couple points to make. One is in regards to offset, If offset isn't addressed in high gain circuits, they will become a problem in high gain amplifiers. With that in mind, a low frequency feedback can be added to greatly stabilize the circuit. Set the time constant of the feedback to be at least 5X the lowest frequency the circuit is expected to see. In the case of an air cannon, the duration of most launches is in the order of 5 to 50 ms, so a low frequency low gain negative feedback with a time constant of over 100 ms should give reasonable settling times. A 500ms to 5 second settling time would be fine for this application with little drift contamination of the result.btrettel wrote:I'm confused as to why I'd do that. Perhaps I'm using the wrong terminology. I'll explain what I'm doing in a little more detail.
The transfer function for the microphone input is H(jω) = R / (Zc + R) where R is a resistance and Zc is the complex impedance of the capacitor. I need to make a filter/amplifier than is the inverse of this, so H(jω) = (Zc + R) / R (when these two transfer functions/gains are multiplied together they cancel out). The combination of two op. amps does that. The first one has a transfer function of -(Zc + R) / R and the second one inverts that signal.
Next comment is on the use of a pizzo transducer. It is a high impedance device. Pressure and voltage are related, but under static conditions, it is not a free energy producer (not a constant source of say 50 volts DC when clamped in a vise, so any significant loading is a no-no. For this reason a first stage high impedance input is desirable. Using your op amp in a non-inverting mode is one way to do this as inverting configurations assume an input voltage of zero at the inverting pin that is held at zero with the current in the feedback loop. In a non-inverting mode, it becomes a voltage follower with little to no current drawn from the source. The input voltage divider is the remaining source of input loading.
In high gain op amp circuits, bandwidth (maximum frequency) is inversely related to gain. Use low gain for the high speed event.
Because the impedance issues, leakage currents, and complex waveform you wish to capture, a lower high speed solution may be a better fit for this application. Have you considered a high speed load cell?
Research can be started here.
http://www.google.com/#hl=en&q=high+spe ... mZ_-PL2Zjc
The advantage is most load cells are good down to zero hz. A pump and gauge can be used to create a calibration graph and then the pressure on your high speed event would be not contaminated by high speed drift.
-
- Sergeant Major
- Posts: 3197
- Joined: Wed Mar 28, 2007 9:48 am
- Location: Greenwood, Indiana
- Has thanked: 5 times
- Been thanked: 15 times
- Contact:
That isn't right.btrettel wrote: - The voltage across a piezoelectric element is proportional to the pressure differential, not the derivative of the pressure with respect to time. The wacky fluctuations seen in jimmy's circuit are likely due to a combination of sound, #2, and #3.
The voltage output of a piezo is proportional to the rate of change of the pressure (or the rate of change of the pressure differential).
A piezo sitting on the bench will read zero volts with a high Z DVM. Set a weight on the piezo and the reading will spike up, then down, then eventually dampen out to zero volts. Only a changing pressure causes a voltage output from the piezo.
I really don't see any reason for a separate detector at the muzzle. The extremely fast pressure drop when the round exits the barrel should be a very obvious signal. Of course, if you've got a spare data channel (like a stereo soundcard) then you might as well use it for something.
I've built a very high Z amp for Piezos as well. It isn't all that difficult. A FET instrumentation amp chip (not just a single FET OpAmp) works pretty well. I would recommend replacing the LF351 (which is just a FET OpAmp?) with a chip actually designed as an instrumentation amplifier. I used an INA121, which actually contains three OpAmps and some additional circuitry and costs about $7.
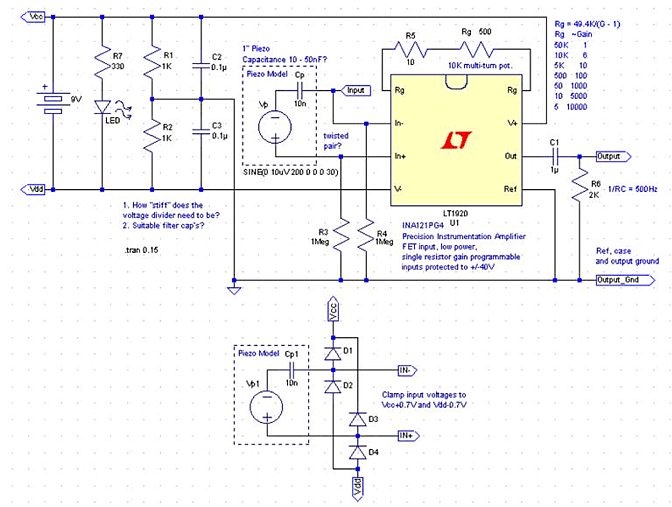
(The schematic shows an different OpAmp because my spice package doesn't include the INA121.) This amp was to boost the signal from a 1" piezo to record the sound of ants walking. The gain is set at 500 but for a pressure transducer you would probably want the gain at 1 or even less. Mostly what the amp is used for is to match the impedance of the piezo to the sound card's input.
You still have the problem of the capacitance of the piezo element making slow pressure changes disappear, especially since you also have to be able to get a useable signal when the rate of pressure change is very high (as in when the ammo exits the barrel). I'm not aware of any way to recreate data when all you've got to work with is 0V, 0V, 0V, 0V, 0V, 0V, 0V, 0V, 0V.
It sounds like you've got a pretty good handle on the problem. Be interesting to see what you can get.

-
- Sergeant Major
- Posts: 3197
- Joined: Wed Mar 28, 2007 9:48 am
- Location: Greenwood, Indiana
- Has thanked: 5 times
- Been thanked: 15 times
- Contact:
Oops, should have added...
The piezo gives a voltage that is proportion to the rate of change of pressure on the piezo.
To get to the actual pressure you have to integrate the voltage versus time signal.
You also have to figure out the correct calibration to convert from VoltSeconds into suitable pressure units.
The piezo gives a voltage that is proportion to the rate of change of pressure on the piezo.
To get to the actual pressure you have to integrate the voltage versus time signal.
You also have to figure out the correct calibration to convert from VoltSeconds into suitable pressure units.

- Technician1002
- Captain
- Posts: 5189
- Joined: Sat Apr 04, 2009 11:10 am
Um you are thinking of magnetic pickups. Piezo is not a rate generator. With a load resistor, the high impedance source makes it behave as a rate generator as the load current integrates the signal.jimmy101 wrote:Oops, should have added...
The piezo gives a voltage that is proportion to the rate of change of pressure on the piezo.
To get to the actual pressure you have to integrate the voltage versus time signal.
You also have to figure out the correct calibration to convert from VoltSeconds into suitable pressure units.
Have you checked the input impedance of the bench DVM lately? Circuit loading will bring the voltage back to zero as the generated voltage bleeds it off.A piezo sitting on the bench will read zero volts with a high Z DVM. Set a weight on the piezo and the reading will spike up, then down, then eventually dampen out to zero volts. Only a changing pressure causes a voltage output from the piezo.
On providing a high impedance load on the piezo, consider using an insulated gate field effect transistor in a source follower configuration. The very high input impedance this would provide will do wonders for the waveform. Be sure to find one with ESD protection. They are very easily blown by static charges. Use full ESD precautions.
I wishing I had posted this before buying some parts! Oh well, I'm sure I'll find other uses for them.
Thanks to everyone who posted.
I'm thinking I should avoid the entire microphone input issue though. Something like this circuit should simplify things greatly.
I also read much of the piezo technical manual here and it says the force on the element is proportional to the voltage. I'm confident that you're mistaken.
Thanks to everyone who posted.
Sounds simple enough.Technician1002 wrote:I have a couple points to make. One is in regards to offset, If offset isn't addressed in high gain circuits, they will become a problem in high gain amplifiers. With that in mind, a low frequency feedback can be added to greatly stabilize the circuit. Set the time constant of the feedback to be at least 5X the lowest frequency the circuit is expected to see. In the case of an air cannon, the duration of most launches is in the order of 5 to 50 ms, so a low frequency low gain negative feedback with a time constant of over 100 ms should give reasonable settling times. A 500ms to 5 second settling time would be fine for this application with little drift contamination of the result.
I'm thinking I should avoid the entire microphone input issue though. Something like this circuit should simplify things greatly.
No, I hadn't considered them. They seem rather expensive though. I intend to keep this a low cost as possible, but if I find a low cost load cell I might start working on a circuit.Technician1002 wrote: Because the impedance issues, leakage currents, and complex waveform you wish to capture, a lower high speed solution may be a better fit for this application. Have you considered a high speed load cell?
Research can be started here.
http://www.google.com/#hl=en&q=high+spe ... High+speed +load&aqi=g1&=Google+Search&=I%27m+Feeling+Lucky&fp=1mZ_-PL2Zjc
The advantage is most load cells are good down to zero hz. A pump and gauge can be used to create a calibration graph and then the pressure on your high speed event would be not contaminated by high speed drift.
I had read your page first and began this project thinking that, but every source I've read says otherwise. I have a book titled "Theory and Design for Mechanical Measurements" by Richard Figliola that say the pressure differential on a piezoelectric element is proportional to its voltage on p. 346 and gives a relationship between voltage and pressure for quartz crystals.jimmy101 wrote:That isn't right.
The voltage output of a piezo is proportional to the rate of change of the pressure (or the rate of change of the pressure differential).
I also read much of the piezo technical manual here and it says the force on the element is proportional to the voltage. I'm confident that you're mistaken.
Worth looking in to. Thanks.jimmy101 wrote:I've built a very high Z amp for Piezos as well. It isn't all that difficult. A FET instrumentation amp chip (not just a single FET OpAmp) works pretty well. I would recommend replacing the LF351 (which is just a FET OpAmp?) with a chip actually designed as an instrumentation amplifier. I used an INA121, which actually contains three OpAmps and some additional circuitry and costs about $7.
I was going to use an op. amp for that. What advantage would the FET have? They have a diagram on p. 38 of the piezo technical manual that is like your suggestion, but give no reason to use it over an op. amp.Technician1002 wrote:On providing a high impedance load on the piezo, consider using an insulated gate field effect transistor in a source follower configuration. The very high input impedance this would provide will do wonders for the waveform. Be sure to find one with ESD protection. They are very easily blown by static charges. Use full ESD precautions.
All spud gun related projects are currently on hold.
- Technician1002
- Captain
- Posts: 5189
- Joined: Sat Apr 04, 2009 11:10 am
The lower the current you draw off the piezo the less circuit drift. In a slow event, you want the piezo output to be completely unloaded so there is no significant TC during your measured event. An insulated gate FET is about as close as you can get to operating the piezo with nothing connected to bleed off the voltage over time. This puts it more into a direct pressure = voltage output instead of rate of change = voltage.I was going to use an op. amp for that. What advantage would the FET have? They have a diagram on p. 38 of the piezo technical manual that is like your suggestion, but give no reason to use it over an op. amp.
Note the leakage currents the op amps have on the inputs. They are not zero current devices. For example you can't use one and measure a charge on a pocket comb by waving it near the input lead. An IGFET can measure the dc charge in air due to it's high impedance/low leakage gate. With a metal bladed fan in front of a voltage probe, this is often used to measure the surface charge of plastics and such. The metal blade is the ground reference, the opening measures the surface charge as the blade rotates chopping the voltage field.
A typical application is like this one.
http://www.takkspecials.com/
-
- Sergeant Major
- Posts: 3197
- Joined: Wed Mar 28, 2007 9:48 am
- Location: Greenwood, Indiana
- Has thanked: 5 times
- Been thanked: 15 times
- Contact:
A couple things;
1. You don't need a high gain amp. You actually will need to reduce the voltage the piezo generates since the sound card input is probably limited to about +/-1V swing. Smack the piezo with just your finger and you'll get several volts even on a DVM. In the combustion chamber it may well generate tens of volts or more when the pressure goes form 0 PSIG to ~60 PSIG in 20mS.
2. You need a high impedance amp. As Tech said the power of the crystal is very low. "High" voltage but almost zero current. If you actually draw any current from the piezo then it's voltage will sag.
That's why you use an FET based opamp. Very high input impedance of about 10^12 ohms. The problem is that at that input impedance things get wonky. In my circuit the input impedance is about 1Meg (set by the two bypass resitors on the input line), which should be high enough for the fairly robust signal that smacking the piezo this hard will produce.
My DVM has 10Meg input impedance. Piezos read 0mV. 10Meg of resitance isn't anywhere near enough resistance to read the static voltage. To measure that voltage you need a "charge amplifier" with an extremely high impedance. A Megaohm won't do it. A Gigaohm probably won't do it. Any resistor over a gigaohm or so is basically worthless since you are in the domain where the air is starting to conduct and shorting around the resistor.
The piezo generates significant voltage and current when it is smacked, just not enough to power a line or MIC input to a soundcard. I believe it is much easier to match that signals impedance to the soundcard input then integrate the signal then it is to just work with the piezos voltage directly and a very high impedance (>10^12ohm) amp. In the first case you are actually measuring the charge generated on the piezo and it is OK to remove that charge in the measuring process. In the second case you are trying to measure the voltage without actually removing any charge.
A piezo sparker generates ~10KV when the crystal is struck. If you set a heavy weight on the piezo it doesn't swing it's two faces up to a 10KV difference then just sit there. The crystal conducts and even without an external circuit the voltage difference goes back to zero once the pressure becomes static.
http://www.piezo.com/tech2intropiezotrans.html
1. You don't need a high gain amp. You actually will need to reduce the voltage the piezo generates since the sound card input is probably limited to about +/-1V swing. Smack the piezo with just your finger and you'll get several volts even on a DVM. In the combustion chamber it may well generate tens of volts or more when the pressure goes form 0 PSIG to ~60 PSIG in 20mS.
2. You need a high impedance amp. As Tech said the power of the crystal is very low. "High" voltage but almost zero current. If you actually draw any current from the piezo then it's voltage will sag.
That's why you use an FET based opamp. Very high input impedance of about 10^12 ohms. The problem is that at that input impedance things get wonky. In my circuit the input impedance is about 1Meg (set by the two bypass resitors on the input line), which should be high enough for the fairly robust signal that smacking the piezo this hard will produce.
My DVM has 10Meg input impedance. Piezos read 0mV. 10Meg of resitance isn't anywhere near enough resistance to read the static voltage. To measure that voltage you need a "charge amplifier" with an extremely high impedance. A Megaohm won't do it. A Gigaohm probably won't do it. Any resistor over a gigaohm or so is basically worthless since you are in the domain where the air is starting to conduct and shorting around the resistor.
The piezo generates significant voltage and current when it is smacked, just not enough to power a line or MIC input to a soundcard. I believe it is much easier to match that signals impedance to the soundcard input then integrate the signal then it is to just work with the piezos voltage directly and a very high impedance (>10^12ohm) amp. In the first case you are actually measuring the charge generated on the piezo and it is OK to remove that charge in the measuring process. In the second case you are trying to measure the voltage without actually removing any charge.
A piezo sparker generates ~10KV when the crystal is struck. If you set a heavy weight on the piezo it doesn't swing it's two faces up to a 10KV difference then just sit there. The crystal conducts and even without an external circuit the voltage difference goes back to zero once the pressure becomes static.
http://www.piezo.com/tech2intropiezotrans.html
DYNAMIC VERSUS STATIC SENSOR OPERATION
Piezo elements are excellent for dynamic or transient motion and force sensing. They are used as strain gages for easy and rapid determination of dynamic strains in structures due to their extremely high signal/noise ratios (on the order of 50 times that of wire strain gages). They require no power input since they generate their own power. In fact, this is why they are now considered useful as energy harvesting and scavenging devices. They are small enough that they will not materially affect the vibrational characteristics of most structures.
On the other hand, piezo elements are generally poor at measuring static or slowly changing inputs due to charge leakage across their electrodes or through monitoring circuits.

-
- Sergeant Major
- Posts: 3197
- Joined: Wed Mar 28, 2007 9:48 am
- Location: Greenwood, Indiana
- Has thanked: 5 times
- Been thanked: 15 times
- Contact:
Since they have leakage current they generally require bias currents on their inputs. In most cases that current is tiny compared to the signal. To read the static voltage from a static piezo that bias current is going to be huge.Technician1002 wrote:Note the leakage currents the op amps have on the inputs. They are not zero current devices. For example you can't use one and measure a charge on a pocket comb by waving it near the input lead.
A plain old FET can easily read the charge on a pocket comb from a couple feet away. (For example http://www.eskimo.com/~billb/emotor/chargdet.html) Indeed, for many circuits an FET is considered to draw zero current. That is true when you are talking about normal current levels down to a couple microamps or even nanoamps. But even a nanoamp is a lot compared to what the piezo can source.

- Technician1002
- Captain
- Posts: 5189
- Joined: Sat Apr 04, 2009 11:10 am
When measuring the high impedance piezo, due to introducing a RC time constant with any resistive divider, a capacitive divider is often used if you need to attenuate the voltage.
Don't worry about the "Filter" cutting the signal and all. A piezo on the high frequency end is a low impedance device. It contains the equivalent of a series capacitance. A capacitive divider works fine with little bandwidth loss due to capacitive loading. the series R value in the circuit is a low value.
Since the value of a random piezo transducer is an unknown, a cut and try approach works fine. Try a 47 pf series with 100 pf in parallel for example if you want approximately a 4:1 divider.
Avoid large values, they load the circuit too much and will shunt it completely.
Don't worry about the "Filter" cutting the signal and all. A piezo on the high frequency end is a low impedance device. It contains the equivalent of a series capacitance. A capacitive divider works fine with little bandwidth loss due to capacitive loading. the series R value in the circuit is a low value.
Since the value of a random piezo transducer is an unknown, a cut and try approach works fine. Try a 47 pf series with 100 pf in parallel for example if you want approximately a 4:1 divider.
Avoid large values, they load the circuit too much and will shunt it completely.