Sheet Metal Tube?
-
- Specialist 2
- Posts: 272
- Joined: Fri May 12, 2006 8:37 pm
- Location: New Brunswick, Canada
Would it be possible to take sheet metal and weld it as a tube and use it for pressure applications?
I know that the metal itself can hold pressure, but how to weld it in a nice tube shape and make the weld strong well....?
Any help would be great.
Thanks
Cannon Freak.
I know that the metal itself can hold pressure, but how to weld it in a nice tube shape and make the weld strong well....?
Any help would be great.
Thanks
Cannon Freak.
- rna_duelers
- Staff Sergeant 3
- Posts: 1739
- Joined: Mon Sep 26, 2005 7:07 am
- Location: G-land Australia
Why not just buy some metal tubing?Plus i dont think you have a pressure vessel welding certificate,or do you?
What thickness sheet metal were you thinking of using?Because i would use a minimum of about 2-2.5mm thickness and that would take a long time to shape and shape it good so it's not an oval.What diametre pipe were you planning on making?
The weld would be the weakest point and unless your are very compitent wiht your skills i wouldnt try it,just buy the tubing already made.
What thickness sheet metal were you thinking of using?Because i would use a minimum of about 2-2.5mm thickness and that would take a long time to shape and shape it good so it's not an oval.What diametre pipe were you planning on making?
The weld would be the weakest point and unless your are very compitent wiht your skills i wouldnt try it,just buy the tubing already made.
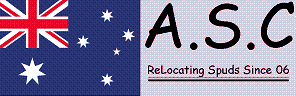
Good point on the metal tubing, but just because he might not be certified to weld a pressure vessel doesn't mean the welds will automatically fail. If he is a really good welder, then the last thing to fail would be the welds, but even if he isn't very good, the welds will still hold way more pressure than most cannons can create. I only learned how to weld a couple months ago, and I'm not an overly amazing welder, but I could make a tube out of sheet metal and as long as the steel is thick enough it would withstand anything you could do to it using fluidic propellants.rna_duelers wrote:Why not just buy some metal tubing?Plus i dont think you have a pressure vessel welding certificate,or do you?
What thickness sheet metal were you thinking of using?Because i would use a minimum of about 2-2.5mm thickness and that would take a long time to shape and shape it good so it's not an oval.What diametre pipe were you planning on making?
The weld would be the weakest point and unless your are very compitent wiht your skills i wouldnt try it,just buy the tubing already made.
- MisterSteve124
- Corporal 3
- Posts: 702
- Joined: Sat Feb 11, 2006 10:11 pm
- Location: West Chester, PA
- Contact:
Yeah I wouldn't make a gun using sheet metal tubing. Sheet metal isn't very strong you can easily bend it with a finger. It would be covered in dents. If you are just making a regular gun that I'd stay stick with pvc but if its going to be powerful then just get real metal tubing.
-
- Specialist 2
- Posts: 272
- Joined: Fri May 12, 2006 8:37 pm
- Location: New Brunswick, Canada
Ya Im not going to make one out of sheet metal, however, you can find out the theoretical bursting pressure of metal tubing, I forget where I had the math but its pretty easy, and no different from how they stick the pressure rating on pressure rated pipe.
The only difference with tubing is that the wall thickness may vary somewhat since its not made at such a high standard so just give yourself a good marjin and your fine.
Cannon Freak.
The only difference with tubing is that the wall thickness may vary somewhat since its not made at such a high standard so just give yourself a good marjin and your fine.
Cannon Freak.
To tell you quite honestly, I don’t know.
"Why not just buy some metal tubing?Plus i dont think you have a pressure vessel welding certificate,or do you?" ~rna_duelers
Wow you really don’t know what your talking about...
The purchase of large bore metal tubing gets rather expensive, and in response his inquiry.
Simply having a certificate means nothing. I mean I have a certificate to take a sh*t in toilets, while you don’t. Does that mean you cant?
Tshylea, on the other hand knows what he’s talking about. If welded correctly, the weld will be stronger then that of the surrounding metal.
Cannon Freak, if you didn’t intend on building such, why did you bring up this thread in the first place...?
Anyway, if anyone were to do such Id suggest either a MIG or TIG welder. I started learning TIG about a month ago for both steel and aluminum (quite a bit difference between the two with the whole Aluminum Oxide deal, and high surface tension). I suggest both the MIG and TIG because neither leave as many imperfections and can be controlled easier. Just when doing the MIG do weld similar to that of when your bridging gaps as to not over heat the metal.
"Why not just buy some metal tubing?Plus i dont think you have a pressure vessel welding certificate,or do you?" ~rna_duelers
Wow you really don’t know what your talking about...
The purchase of large bore metal tubing gets rather expensive, and in response his inquiry.
Simply having a certificate means nothing. I mean I have a certificate to take a sh*t in toilets, while you don’t. Does that mean you cant?
Tshylea, on the other hand knows what he’s talking about. If welded correctly, the weld will be stronger then that of the surrounding metal.
Cannon Freak, if you didn’t intend on building such, why did you bring up this thread in the first place...?
Anyway, if anyone were to do such Id suggest either a MIG or TIG welder. I started learning TIG about a month ago for both steel and aluminum (quite a bit difference between the two with the whole Aluminum Oxide deal, and high surface tension). I suggest both the MIG and TIG because neither leave as many imperfections and can be controlled easier. Just when doing the MIG do weld similar to that of when your bridging gaps as to not over heat the metal.
Doing it like that with MIG would take hours though. If you know what you are doing I'm guessing you could do a foot in about 5 minutes depending on the metal's thickness. So much easier just to buy a tube.pimpmann22 wrote:To tell you quite honestly, I don’t know.
"Why not just buy some metal tubing?Plus i dont think you have a pressure vessel welding certificate,or do you?" ~rna_duelers
Wow you really don’t know what your talking about...
The purchase of large bore metal tubing gets rather expensive, and in response his inquiry.
Simply having a certificate means nothing. I mean I have a certificate to take a sh*t in toilets, while you don’t. Does that mean you cant?
Tshylea, on the other hand knows what he’s talking about. If welded correctly, the weld will be stronger then that of the surrounding metal.
Cannon Freak, if you didn’t intend on building such, why did you bring up this thread in the first place...?
Anyway, if anyone were to do such Id suggest either a MIG or TIG welder. I started learning TIG about a month ago for both steel and aluminum (quite a bit difference between the two with the whole Aluminum Oxide deal, and high surface tension). I suggest both the MIG and TIG because neither leave as many imperfections and can be controlled easier. Just when doing the MIG do weld similar to that of when your bridging gaps as to not over heat the metal.
-
- Specialist 2
- Posts: 272
- Joined: Fri May 12, 2006 8:37 pm
- Location: New Brunswick, Canada
Cannon Freak, if you didn’t intend on building such, why did you bring up this thread in the first place...?
I brought this up a while ago when I WAS PLANNING on doing it, however, after thinking about it, your right, just to much trouble, and peoples minds change over time especially when they just rush into something as I did.
I personally was not going to be doing the welding my grandfather was going to, who has had over 40+ years of welding experience, including pressure vessels, however he was away and I decided to post here.
Anyway Ill just be getting the tubing.
Cannon Freak.
It doesn't take hours, mig welding is actually a whole lot faster then many other types of welding(takes me less then 2 minutes to weld a foot), and in my personnel opinion more reliable and easier to learn and do. Ive been doing it for three years and have welded several pressure vessels all able to withatnd 600 psi (never tested them any higher.) and the first one i welded was only 3 months after i had learned how to weld.Tshylea wrote:
Doing it like that with MIG would take hours though. If you know what you are doing I'm guessing you could do a foot in about 5 minutes depending on the metal's thickness. So much easier just to buy a tube.
Even though Cannon freak says he isnt gonna do it anymore, for anyone whos looking into welding, its a fun extremely usfull hobby, and usually is pretty easy to learn and is a great way to make large daimeter preesure chambers relatively cheaply.
If your material was thick enough and you could run a solid bead then ya it would go quickly, but if you are using really thin sheet metal you would have to.... I'm not sure the technical way to say it, but you would have to make a whole bunch of tacks, all connected and touching each other. Last month I had a ski-doo exhaust pipe with a big dent in it. I cut it open, hammered the dent out and welded the piece back on. It took me almost 2 hours to weld it using that on-off technique and there was probably only 3 feet of welding done.Killjoy wrote:It doesn't take hours, mig welding is actually a whole lot faster then many other types of welding(takes me less then 2 minutes to weld a foot), and in my personnel opinion more reliable and easier to learn and do. Ive been doing it for three years and have welded several pressure vessels all able to withatnd 600 psi (never tested them any higher.) and the first one i welded was only 3 months after i had learned how to weld.Tshylea wrote:
Doing it like that with MIG would take hours though. If you know what you are doing I'm guessing you could do a foot in about 5 minutes depending on the metal's thickness. So much easier just to buy a tube.
Even though Cannon freak says he isnt gonna do it anymore, for anyone whos looking into welding, its a fun extremely usfull hobby, and usually is pretty easy to learn and is a great way to make large daimeter preesure chambers relatively cheaply.
with me, my welder has an adjustable output so all i have to do is lower the output power and can run a conitnous beed no prob on sheet metal. Also, i use 18 gauge sheet metal which has no problem standing up to pressure and also i can weld it with the highest setting on my welder without melting it badly (not that i do) and still be able to run a continous bead. If you move fast enough, you should be able to to run a continous bead no problem. But ive been welding awhile so ive got this rythem thing down that alwos me to move fast and a get a good weld.
If the choice was between MIG and Oxy-Acetylene welding, which one would be better? I can do both pretty well. Oxy-Acetylene is slower, but I prefer it to MIG just because my welds look much better, and actually probably are better. I am not talking about brazing with brass rod and flux, I'm talking about using steel wire and melting the two peices together with the addition of the wire.