Page 1 of 2
Epoxy casting/use
Posted: Mon May 31, 2010 12:35 pm
by Slauma
I've been working on a new golfball gun and in an effort to ergonomize I've been trying to figure out the best way to reduce (hopefully eliminate) the distance between the chamber and the barrel while maintaining the pressure bearing capability/functionality of the valve. The valve will be used at 60-120 psi and is a typical barrel sealing piston housed in a 2" tee, very similiar to the GB gun seen
here. Just to be clear what I'm speaking of here is a picture courtesy of unisonmind
Originally I thought using a street elbow (male x female) like this

as opposed to a normal elbow (female x female) would help this problem, but as you can see on unisonmind's cannon this is exactly what he did and it still left enough room to use 2.5" pvc as the chamber and and still have about an inch of clearance.
So, onto my questions. I've never really worked with epoxy before and I'd like to know if I were to remove part of these fittings to give them a closer fit could I then seal it all together inside a block of epoxy and it could withstand at least 60-120 psi? Here's a picture I threw together to illustrate.
My next question is what kind of epoxy would be best for something like this? It would require a fairly large amount (6" x 6" x 3" block = 108ci, so 108ci minus the volume of the fittings), more than comes in any of the syringe type epoxies I've seen. I've seen the sailing/boat epoxy that comes in a large metal can but I'm not exactly sure where I could buy that. Lastly, once the epoxy had cured would there be any problem sanding it down? Just to remove edges and corners and such.
I know epoxy is fairly widely used in spud construction, particularly for pistons, but I'm not very familiar with its characteristics and how well it would work for things other than pistons. I'm almost positive I've seen a member here on spudfiles who has used this or similar methods (casting housings out of epoxy) in their cannons but I can't find anything about it now and the search function isn't much help.
[/url]
Posted: Mon May 31, 2010 8:46 pm
by jor2daje
JSR is very well known for his epoxy casting, he makes everything from it.
here is his how to that he wrote, hope that helps. Not really sure why you want to eliminate that space so badly
Posted: Mon May 31, 2010 8:47 pm
by Gun Freak
Without doing the epoxy, get a street elbow then use 45 degree elbows to make the chamber higher like I did on Superna.
Posted: Mon May 31, 2010 8:56 pm
by clemsonguy1125
Just a street elbow is what I use on a couple of my unposter guns
Re: Epoxy casting/use
Posted: Mon May 31, 2010 8:58 pm
by Gun Freak
Slauma wrote:I've been trying to figure out the best way to reduce (hopefully eliminate) the distance between the chamber and the barrel
Clemsonguy he can't just use a street elbow, but I have a feeling that in combo with the street elbow he can use two 45 degree elbows to move the chamber up higher.
Posted: Mon May 31, 2010 9:18 pm
by clemsonguy1125
That would move the chamber too far up and the there would be no room for the barrel, you could use a street elbow and a 3 inch chamber
Posted: Mon May 31, 2010 9:21 pm
by Technician1002
It's OK to simply extend the chamber diameter to include the T at the chamber diameter. Put a 3inch to 2 inch reducer in each side of the T and pretend it is a 2 inch T. This provides very little airflow restriction from the chamber to the valve. This is almost as good as a coaxial like the ones I build.
The 3 inch T, chamber and elbow add considerable strength to the launcher. Without the smaller parts, it is less likely to get broken.
Forget the epoxy. The heaver sturdy parts will not only look better, but will improve performance. The 3 inch parts can be substituted with 4 inch for a very short compact chamber. My Marshmallow cannon does nice things with golf balls even with a very short chamber.
Posted: Mon May 31, 2010 10:29 pm
by Gaderelguitarist
I would actually look forward to the result of casting those parts in an epoxy block.
I understand your want for an aesthetically pleasing build, and the closeness of your barrel and chamber. I too have suffered these dilemmas. I just don't have enough epoxy or patience to cast it.
Use a strong two part epoxy. You want one that will cure with a good measure of impact and torsion/shear resistance. Then when you cast, make sure to rough up the outer portions of the fittings so that the epoxy might bond more securely. Then just mock up a mold and you'll be set to mix and pour.
Posted: Mon May 31, 2010 10:32 pm
by Lockednloaded
i would use two 45s to get the chamber closer along with a 90 degree elbow, I've got a launcher in the works right now, the chamber's all set up i can show a picture if you want..
Posted: Mon May 31, 2010 10:50 pm
by Slauma
That's who it was I had seen jor2daje, thanks for the link.
Gun Freak wrote:Without doing the epoxy, get a street elbow then use 45 degree elbows to make the chamber higher like I did on Superna.
This is actually the last upgrade I made to my most recent gun. I personally just don't like it as much this way, it still feels too bulky and it doesn't fit well in the design of the rest of the gun. Plus I ran into some troubles glueing all the joints and ended up with a chamber quite a bit off from being parallel with the barrel; that was just me being stupid though.
@Tech
I'm having a little bit of trouble picturing what you're talking about. Think you could whip up a diagram? Visuals seriously help me, you should see all the little sketches on all the random bits of paper scattered about my desk
Posted: Mon May 31, 2010 11:20 pm
by Technician1002
Slauma wrote:
@Tech
I'm having a little bit of trouble picturing what you're talking about. Think you could whip up a diagram? Visuals seriously help me, you should see all the little sketches on all the random bits of paper scattered about my desk
OK. It's quick as I just used Paint at work. I miss the Gimp here..
Beef up the elbow indicated with 3 inch to the valve and beef up the valve to a 3 inch shell using a large T. Use the reducers to build the 2 inch valve inside. Flow is now unrestricted from the chamber to the valve.
Now the chamber bends full size right into the piston. The elbow and T become part of the chamber.
Posted: Tue Jun 01, 2010 12:45 am
by jackssmirkingrevenge
Have a look at
this project.
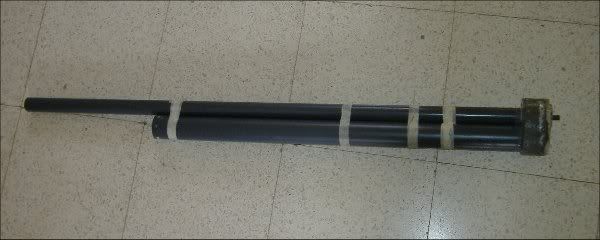
Posted: Tue Jun 01, 2010 8:12 pm
by Slauma
Precisely the man I'm looking for apparently.
Very helpful, thank you.
I'm gonna go ahead and start modifying the fittings to try this I think. Did you use
this stuff you linked to on ebay on that cannon? Do they make special high pressure epoxies? The only thing I've seen that's more than just a little tube is the brand x type stuff like what you linked to on ebay. How high have you taken the pressure on that cannon and what do you think it could handle?
EDIT: actually, now that I look more closely at the stuff you linked to on ebay I can see that seems fairly legit, I didn't see all the stuff they have in the description
Posted: Tue Jun 01, 2010 8:15 pm
by Gun Freak
Slauma if you look closely at Superna, I did screw up on the allignment of the 45* elbows resulting in the chamber and barrel not being parallel, but it is very subtle when the barrel is on.
Posted: Tue Jun 01, 2010 8:50 pm
by Slauma
Gun Freak wrote:Slauma if you look closely at Superna, I did screw up on the allignment of the 45* elbows resulting in the chamber and barrel not being parallel, but it is very subtle when the barrel is on.
Mine wasn't too bad either. Actually when I put hose clamps around the barrel and chamber for the barrel support I could tighten down the hose clamps and you couldn't even tell because it pulled the barrel and chamber together. I didn't like the idea of putting the extra stress on my PVC like that though.