copper is infinitley safer than PVC....Floyd wrote:For a pneumatic if cost doesn't matter, copper. If cost does matter, PVC.
Overall I would recommend PVC because if you use all pressure rated pipe and fittings it will withstand higher than most bike pumps can pump to.
But if you have a high pressure source go for copper.
Piston valve
- ALIHISGREAT
- Staff Sergeant 3
- Posts: 1778
- Joined: Sat Aug 25, 2007 6:47 pm
- Location: UK
<a href="http://www.bungie.net/stats/halo3/defau ... player=ALI H IS GREAT"><img src="http://www.bungie.net/card/halo3/ALI H IS GREAT.ashx"></a>
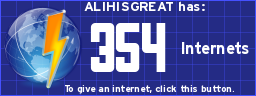
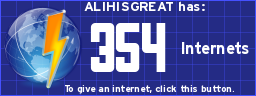
- Gippeto
- First Sergeant 3
- Posts: 2504
- Joined: Sat Jan 19, 2008 10:14 am
- Location: Soon to be socialist shit hole.
- Has thanked: 2 times
- Been thanked: 17 times
You need to think about how you are going to join the dissimilar metals.
You cannot solder, braze, or weld aluminum to copper or iron/steel.
Welding aluminum to aluminum requires special skills and tools.
Epoxy can work very well if done properly.
I find copper to be easy to work with and an excellent choice for a building material. Solder is my preferred method of joining it.
Don't bother brazing copper. The temperatures required to braze copper actually anneal the metal, and lower the pressure rating of the tube. Stick with solder and flux.
To put it plainly, the tube will rupture long before a properly soldered joint fails(calculated failure pressure), even with 50/50 lead/antimony solder.
There are several excellent copper piston guns in the pneumatic showcase section. Have a look, and see what you like.
If you decide to work with copper, download the copper tube handbook and give it a read.
http://www.copper.org/publications/pub_ ... ndbook.pdf
You cannot solder, braze, or weld aluminum to copper or iron/steel.
Welding aluminum to aluminum requires special skills and tools.
Epoxy can work very well if done properly.
I find copper to be easy to work with and an excellent choice for a building material. Solder is my preferred method of joining it.
Don't bother brazing copper. The temperatures required to braze copper actually anneal the metal, and lower the pressure rating of the tube. Stick with solder and flux.
To put it plainly, the tube will rupture long before a properly soldered joint fails(calculated failure pressure), even with 50/50 lead/antimony solder.
There are several excellent copper piston guns in the pneumatic showcase section. Have a look, and see what you like.
If you decide to work with copper, download the copper tube handbook and give it a read.
http://www.copper.org/publications/pub_ ... ndbook.pdf
"It could be that the purpose of your life is to serve as a warning to others" – unknown
Liberalism is a mental disorder, reality is it's cure.
Liberalism is a mental disorder, reality is it's cure.
- MrCrowley
- Moderator
- Posts: 10078
- Joined: Fri Jun 23, 2006 10:42 pm
- Location: Auckland, New Zealand
- Been thanked: 3 times
I think it'd be easier just to use threaded fittingsYou need to think about how you are going to join the dissimilar metals.
You cannot solder, braze, or weld aluminum to copper or iron/steel.
Welding aluminum to aluminum requires special skills and tools.
Epoxy can work very well if done properly

- Gippeto
- First Sergeant 3
- Posts: 2504
- Joined: Sat Jan 19, 2008 10:14 am
- Location: Soon to be socialist shit hole.
- Has thanked: 2 times
- Been thanked: 17 times
Quite true, and a good point. 

"It could be that the purpose of your life is to serve as a warning to others" – unknown
Liberalism is a mental disorder, reality is it's cure.
Liberalism is a mental disorder, reality is it's cure.
- john bunsenburner
- Sergeant 5
- Posts: 1446
- Joined: Sun Oct 19, 2008 5:13 am
so should i tap all my pipes or is that too much work? I just like alli barrels becuase they are thicker than the copper ones and also seem straiter(thats my hardware store). I cant really get any threded pipes here.
- POLAND_SPUD
- Captain
- Posts: 5402
- Joined: Sat Oct 13, 2007 4:43 pm
- Been thanked: 1 time
IMO the best thing you can do is to use malleable threaded fittings and pipes for the chamber and stuff.. by doing so you can:
1. play with your design - if you don't like it you can complettely rearrange it in several minutes
2. lower costs - becasue you can use all the parts you bought for your future projects
ohhh and use a copper/aluminium pipe for a barrel and join it to the rest of the gun via a compression fitting...
1. play with your design - if you don't like it you can complettely rearrange it in several minutes
2. lower costs - becasue you can use all the parts you bought for your future projects
ohhh and use a copper/aluminium pipe for a barrel and join it to the rest of the gun via a compression fitting...
Children are the future
unless we stop them now
unless we stop them now