Piston valve
- john bunsenburner
- Sergeant 5
- Posts: 1446
- Joined: Sun Oct 19, 2008 5:13 am
I know the topic was and is discussed over and over again but i have to admit that i simply do not understand how a Piston valve works, nor do i quite understand how they are built. I think i understand certain concepts about Piston valves but i dont want to get anythign wrong, therefore i am asking for some one, most probably far more expierienced than me, to explain the principles of operation and the prinicples of constuction as well as the materils needed to do the latter. Thank you in advanced for yur help.
- potatoflinger
- Sergeant 2
- Posts: 1136
- Joined: Thu Nov 02, 2006 3:26 pm
- Location: Maryland
First, read the title of the section you posted this topic in, then take a look at this. You could also look for "piston valves explained visually".
It's hard to soar with eagles when you're working with turkeys.
- Pilgrimman
- Specialist 4
- Posts: 480
- Joined: Thu Jun 28, 2007 1:10 pm
- Location: Grants Pass, OR
Here is somewhat of an explanation:
The piston is green, and the air is blue. The sealing face is red. The sealing face is what keeps the air from flowing into the barrel. It has the same function as a weather seal on a door, or anything that is meant to be airtight. Now notice how the pilot/fill area is behind the piston. When you begin filling, the air pushes the piston forward, and seals it against the barrel. Notice, however, that the piston is not a PERFECT fit in the housing. This is to allow air to flow to the rest of the gun once the barrel is sealed off. This is one of the pitfalls of filling slowly: you might just leak air past the piston without moving it. That is why a high-volume bike pump or an air compressor are popular filling methods. Now that the piston is sealed, you fill until you have reached your desired pressure.
Why, you might ask, does the piston stay sealed if there is equal pressure on both sides?
This is all down to the interplay of forces. In physics (Don't know if you have had it or not) you will learn that Pressure is equivalent to Force distributed over an Area. Pressure has SI units of Pascals (Newtons per Square Meter), but we use Pounds per Square Inch in America. Again:
P = F/A
Now that you know this, take a look at the piston again: Notice how there are unequal areas of the piston exposed to pressure? The pilot (back) end of the piston has all of the surface area exposed. The side sealing the barrel only has the part that is bigger than the barrel exposed.
Now, we know the pressure is equal on both sides. (For the sake of ease, let's assume that the area on the pilot side is 2 square inches and the barrel surface area is 1 square inch, and the pressure is 100 psi)
Pilot side: 100 = F/2
Barrel side: 100 = F/1
when you solve for F, you find out that on the pilot side you have 200 pounds of force pushing the piston against the barrel, and only 100 pounds pushing it away from the barrel. This is what seals the piston. Now what would happen if you got rid of the air in the pilot area? You guessed it: There would be no force pushing the piston against the barrel. Now, you might imagine that due to the piston not fitting perfectly in the housing that ALL the air would leak out. This is not true, simply due to the fact that there is so little area for the air to flow out. The force on the barrel side of the piston is now more than the force on the pilot side (0) so the piston is PUSHED (not pulled or sucked, a common misconception) back, exposing the barrel, which allows much more air to flow than the small hole between the piston and the housing.
If you slogged through that, I still have more.
If you are concerned about the performace of your gun, you will be concerned with piston travel, or how far your piston moves back when it opens. The effort that the air exerts to push the piston back is known as work. Ideally, you want all the work to be done on the projectile, but you must open the piston. You also want the piston to be open enough that the airflow is not constricted. It's like blowing through a straw as opposed to a syringe. The straw allows air to flow easier. So the ultimate situation is a piston that opens enough to allow unconstricted airflow, but still maximizes the work done on the projectile. Work is given by force times distance (if the force and distance are in line. Strictly, it is given by F*D, with "*" meaning the vector dot product) So the more your piston moves back, the more work is done on the piston that could be done on the projectile. Now think in terms of flow. If you want full flow, you want the cross sectional area of your barrel to be equal to the area exposed by the piston. A better explanation may be found here: (from the wiki, made by me
)
In both cases, provided there is a good deal of space around the barrel, the full flow potential of the valve is realized when the piston has moved back 1/4th of the barrel's inside diameter (I.D./4). The derivation of this formula is as follows:
Given: A = Pi(R)^2
C = 2PiR
T = Piston travel
R = I.D. of barrel / 2
When the piston moves back, the smallest amount of area exposed is either the area of the circular cross section of the barrel or the area exposed by the piston, which is the side of a cylinder, the bases being the barrel and piston face. The optimal ratio of area exposed between the 2 spots is 1:1, which means the exposed areas should be the same. So one sets the equations A and CT equal, that is A = CT.
Pi(R)^2 = 2PiR(T)
Solving for "T" results in:
R/2 = T which, if one substitutes I.D./2 for R, results in:
I.D./4 = T
This means that the optimal piston travel is the inner diameter of your barrel divided by 4.
Another aspect of design is the bumper. As in the example, you can see that the air exerts a lot of force on the piston. This force is more than capable of cracking PVC in most cases. This is why a bumper is put in the back, where the piston slams. This can be any absorbent material, such as half a tennis ball, or maybe a piece of hose. Another benefit of having a bumper is that it takes up some of the pilot volume, which makes your gun perform better. Why? Read on:
The pilot volume is the area that gets exhausted to open the piston. As you can imagine, if there is a lot of pilot volume to get rid of, it takes longer. This can be counteracted in 3 ways: 1) minimize pilot volume 2) Get a faster opening pilot valve (the valve that exhausts the pilot area, usually a ball or sprinkler valve), or 3) Get a valve with a higher flow rate (more area for air to flow). Ideally, you want all 3: A small pilot volume, and a fast valve with a high flow rate. For this reason, I use a QEV (which is essentially a commercially made piston valve) to pilot, and I make my piston as light as possible. Since force is Mass time acceleration, as you may imagine, a heavy piston will accelerate slower than a light one under the same force.
One other major aspect exists in piston design: The size of the housing in relation to the barrel. You might think you would want a bigger housing so that there is more force on the barrel side. Imagine a 3" tee with a 1/2" barrel. There is a lot of force on the barrel side. But now consider the pilot side: The size of the tee means the pilot vloume is now larger. The piston will move back faster, but the pilot volume is also larger. This is one of the major factors in piston design. If you use, say, a 1 1/2" tee with a 1 1/4" barrel, there won't be much surface area on the front of the piston, so it won't open as fast. However, the pilot volume is small, since the tee is as small as possible.
If any of this confuses you, PM me. I know it was a little long-winded.
Trust me, this knowledge will truly come with experience. It is really rewarding the first time you hear that BOOM! that means your piston opened
The piston is green, and the air is blue. The sealing face is red. The sealing face is what keeps the air from flowing into the barrel. It has the same function as a weather seal on a door, or anything that is meant to be airtight. Now notice how the pilot/fill area is behind the piston. When you begin filling, the air pushes the piston forward, and seals it against the barrel. Notice, however, that the piston is not a PERFECT fit in the housing. This is to allow air to flow to the rest of the gun once the barrel is sealed off. This is one of the pitfalls of filling slowly: you might just leak air past the piston without moving it. That is why a high-volume bike pump or an air compressor are popular filling methods. Now that the piston is sealed, you fill until you have reached your desired pressure.
Why, you might ask, does the piston stay sealed if there is equal pressure on both sides?
This is all down to the interplay of forces. In physics (Don't know if you have had it or not) you will learn that Pressure is equivalent to Force distributed over an Area. Pressure has SI units of Pascals (Newtons per Square Meter), but we use Pounds per Square Inch in America. Again:
P = F/A
Now that you know this, take a look at the piston again: Notice how there are unequal areas of the piston exposed to pressure? The pilot (back) end of the piston has all of the surface area exposed. The side sealing the barrel only has the part that is bigger than the barrel exposed.
Now, we know the pressure is equal on both sides. (For the sake of ease, let's assume that the area on the pilot side is 2 square inches and the barrel surface area is 1 square inch, and the pressure is 100 psi)
Pilot side: 100 = F/2
Barrel side: 100 = F/1
when you solve for F, you find out that on the pilot side you have 200 pounds of force pushing the piston against the barrel, and only 100 pounds pushing it away from the barrel. This is what seals the piston. Now what would happen if you got rid of the air in the pilot area? You guessed it: There would be no force pushing the piston against the barrel. Now, you might imagine that due to the piston not fitting perfectly in the housing that ALL the air would leak out. This is not true, simply due to the fact that there is so little area for the air to flow out. The force on the barrel side of the piston is now more than the force on the pilot side (0) so the piston is PUSHED (not pulled or sucked, a common misconception) back, exposing the barrel, which allows much more air to flow than the small hole between the piston and the housing.
If you slogged through that, I still have more.
If you are concerned about the performace of your gun, you will be concerned with piston travel, or how far your piston moves back when it opens. The effort that the air exerts to push the piston back is known as work. Ideally, you want all the work to be done on the projectile, but you must open the piston. You also want the piston to be open enough that the airflow is not constricted. It's like blowing through a straw as opposed to a syringe. The straw allows air to flow easier. So the ultimate situation is a piston that opens enough to allow unconstricted airflow, but still maximizes the work done on the projectile. Work is given by force times distance (if the force and distance are in line. Strictly, it is given by F*D, with "*" meaning the vector dot product) So the more your piston moves back, the more work is done on the piston that could be done on the projectile. Now think in terms of flow. If you want full flow, you want the cross sectional area of your barrel to be equal to the area exposed by the piston. A better explanation may be found here: (from the wiki, made by me

In both cases, provided there is a good deal of space around the barrel, the full flow potential of the valve is realized when the piston has moved back 1/4th of the barrel's inside diameter (I.D./4). The derivation of this formula is as follows:
Given: A = Pi(R)^2
C = 2PiR
T = Piston travel
R = I.D. of barrel / 2
When the piston moves back, the smallest amount of area exposed is either the area of the circular cross section of the barrel or the area exposed by the piston, which is the side of a cylinder, the bases being the barrel and piston face. The optimal ratio of area exposed between the 2 spots is 1:1, which means the exposed areas should be the same. So one sets the equations A and CT equal, that is A = CT.
Pi(R)^2 = 2PiR(T)
Solving for "T" results in:
R/2 = T which, if one substitutes I.D./2 for R, results in:
I.D./4 = T
This means that the optimal piston travel is the inner diameter of your barrel divided by 4.
Another aspect of design is the bumper. As in the example, you can see that the air exerts a lot of force on the piston. This force is more than capable of cracking PVC in most cases. This is why a bumper is put in the back, where the piston slams. This can be any absorbent material, such as half a tennis ball, or maybe a piece of hose. Another benefit of having a bumper is that it takes up some of the pilot volume, which makes your gun perform better. Why? Read on:
The pilot volume is the area that gets exhausted to open the piston. As you can imagine, if there is a lot of pilot volume to get rid of, it takes longer. This can be counteracted in 3 ways: 1) minimize pilot volume 2) Get a faster opening pilot valve (the valve that exhausts the pilot area, usually a ball or sprinkler valve), or 3) Get a valve with a higher flow rate (more area for air to flow). Ideally, you want all 3: A small pilot volume, and a fast valve with a high flow rate. For this reason, I use a QEV (which is essentially a commercially made piston valve) to pilot, and I make my piston as light as possible. Since force is Mass time acceleration, as you may imagine, a heavy piston will accelerate slower than a light one under the same force.
One other major aspect exists in piston design: The size of the housing in relation to the barrel. You might think you would want a bigger housing so that there is more force on the barrel side. Imagine a 3" tee with a 1/2" barrel. There is a lot of force on the barrel side. But now consider the pilot side: The size of the tee means the pilot vloume is now larger. The piston will move back faster, but the pilot volume is also larger. This is one of the major factors in piston design. If you use, say, a 1 1/2" tee with a 1 1/4" barrel, there won't be much surface area on the front of the piston, so it won't open as fast. However, the pilot volume is small, since the tee is as small as possible.
If any of this confuses you, PM me. I know it was a little long-winded.
Trust me, this knowledge will truly come with experience. It is really rewarding the first time you hear that BOOM! that means your piston opened

- Attachments
-
- pistonvalvevisual.jpg (26.97 KiB) Viewed 2906 times
Yeah, we wouldn't want to anger the bees, now would we??
I HATE YOU BEES! I HATE YOU BEES! I HATE YOU BEES!
LMAO Classic!!!! I love Family Guy!
I HATE YOU BEES! I HATE YOU BEES! I HATE YOU BEES!
LMAO Classic!!!! I love Family Guy!
- MrCrowley
- Moderator
- Posts: 10078
- Joined: Fri Jun 23, 2006 10:42 pm
- Location: Auckland, New Zealand
- Been thanked: 3 times
- john bunsenburner
- Sergeant 5
- Posts: 1446
- Joined: Sun Oct 19, 2008 5:13 am
Ok first of ally i thank everybody who commented. All comments posted were extremly helpful. I think i understood how a pinston works now, atlead i have a feeling i know what i would have to build. But i still have two concerns:
1. some one mentioned PVC but i was thinking of making my gun from copper and aluminium(tell me if these choices are bad!). Now my question is, do i still have to make my piston from PVC or can i use something more durable, in other words: What things do you ussally make your pistons from?
2. As mentioned above i want to make my gun fom Copper and Aluminium. Aluminium will serve as my barrel while Copper will be what i want to use for pretty much everything alse. My only question(which has parts a. and b.)is:
A. Do these materials work with pistons valves(every one talks about PVC)?
and
B. Can i build my chamber from these materials too?
Thanks in advance for all you help
1. some one mentioned PVC but i was thinking of making my gun from copper and aluminium(tell me if these choices are bad!). Now my question is, do i still have to make my piston from PVC or can i use something more durable, in other words: What things do you ussally make your pistons from?
2. As mentioned above i want to make my gun fom Copper and Aluminium. Aluminium will serve as my barrel while Copper will be what i want to use for pretty much everything alse. My only question(which has parts a. and b.)is:
A. Do these materials work with pistons valves(every one talks about PVC)?
and
B. Can i build my chamber from these materials too?
Thanks in advance for all you help
- ALIHISGREAT
- Staff Sergeant 3
- Posts: 1778
- Joined: Sat Aug 25, 2007 6:47 pm
- Location: UK
copper is fine for pressure... and aluminium too... well the right kinds are anyway. just look at all the copper piston valved cannons in the showcase!
<a href="http://www.bungie.net/stats/halo3/defau ... player=ALI H IS GREAT"><img src="http://www.bungie.net/card/halo3/ALI H IS GREAT.ashx"></a>
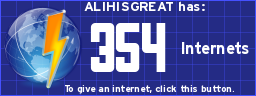
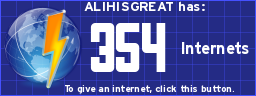
- john bunsenburner
- Sergeant 5
- Posts: 1446
- Joined: Sun Oct 19, 2008 5:13 am
Any do you recoment making the chambre thicker than the rest or not?
- ALIHISGREAT
- Staff Sergeant 3
- Posts: 1778
- Joined: Sat Aug 25, 2007 6:47 pm
- Location: UK
just use regular plumbing copper... and solder it... you don't need special copper.
<a href="http://www.bungie.net/stats/halo3/defau ... player=ALI H IS GREAT"><img src="http://www.bungie.net/card/halo3/ALI H IS GREAT.ashx"></a>
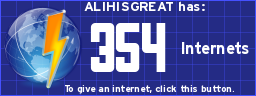
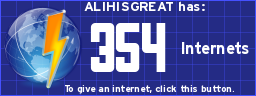
- john bunsenburner
- Sergeant 5
- Posts: 1446
- Joined: Sun Oct 19, 2008 5:13 am
Soldering is the best meathod of connection correct?
- john bunsenburner
- Sergeant 5
- Posts: 1446
- Joined: Sun Oct 19, 2008 5:13 am
And what material is the best(i like metal!). Like overall what would you recoment?
For a pneumatic if cost doesn't matter, copper. If cost does matter, PVC.
Overall I would recommend PVC because if you use all pressure rated pipe and fittings it will withstand higher than most bike pumps can pump to.
But if you have a high pressure source go for copper.
Overall I would recommend PVC because if you use all pressure rated pipe and fittings it will withstand higher than most bike pumps can pump to.
But if you have a high pressure source go for copper.
- john bunsenburner
- Sergeant 5
- Posts: 1446
- Joined: Sun Oct 19, 2008 5:13 am
what about alli and iron?
- daberno123
- Corporal
- Posts: 594
- Joined: Mon Nov 19, 2007 5:56 pm
- Location: Ohio
Aluminum and iron are fine choices, but as Floyd pointed out, they cost more. It depends on how much you're willing to spend. There really is no "best" material, it all depends on your gun.
What is the highest pressure and desired bore of your planned gun? Knowing this will eliminate certain materials and help us assist you in choosing a material.
What is the highest pressure and desired bore of your planned gun? Knowing this will eliminate certain materials and help us assist you in choosing a material.