I didn't feel like going down the fridge pump route, it feels kind of like cheating not to mention reliance on the national grid, environmental terrorism, and just plain lazy (I can say that, I only have a small chamber to fill

the pump:
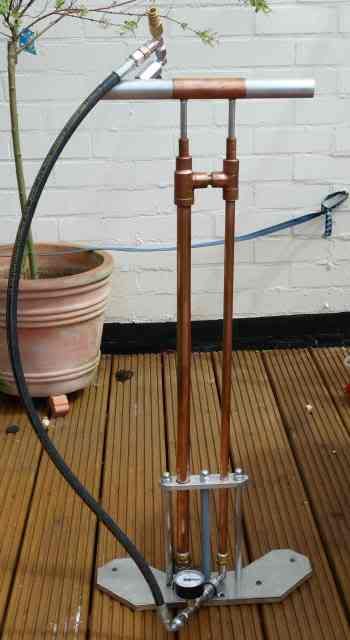
It is a two stage design which I have taken up to 600psi so far without any difficulty, I'm sure it could go higher but I'm worried about deforming the copper, and don't have the right gauge, nor any reason to, yet.
the 1st stage is a length of 22mm OD copper, on the upstroke this is compressed into a smaller 15mm OD cylinder before being further compressed on the downstroke. The idea here is to combine the ease of pumping of the 15mm cylinder with the larger volume of the 22mm cylinder:
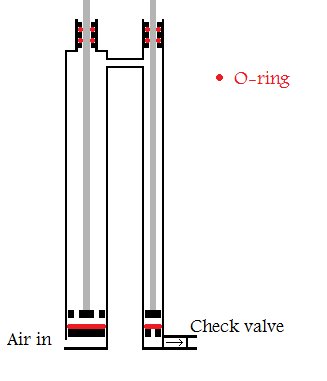
one piston is aluminium the other brass (just what i could find) both turned on my pillar drill. Both use floating o-rings which allow air flow in one direction, each in opposing directions:
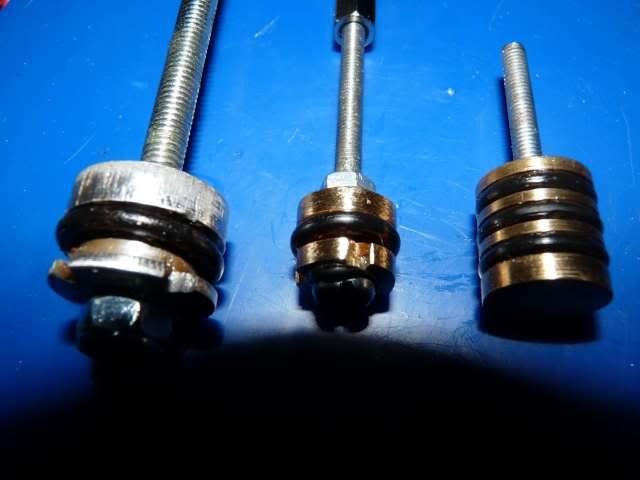
(NOTE: the shaft on the 22mm piston is reversed in the pump, the piston on the right is for a separate project)
the piston shafts are M6 steel rod epoxy sleeved with 3/8 aluminium tube. The base fittings are solder fittings, the top fittings are push fit for servicability. The shaft seals are a collection of o-rings and spacer rings all crimped into sections of 22mm copper with the help of a 'pipe cutter':
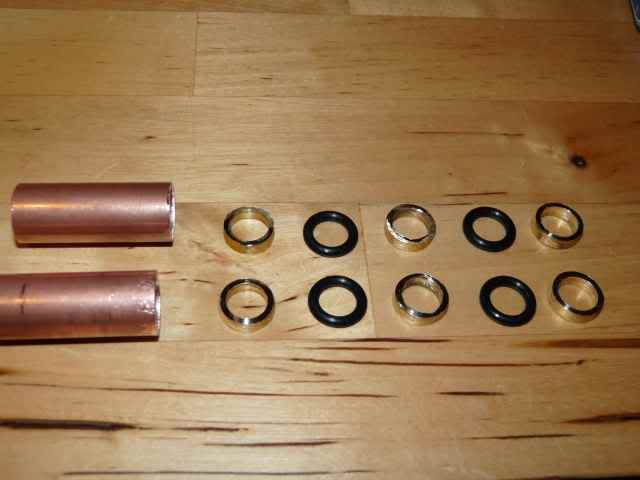
The check valve was the only part of the build which gave me any hassle, I splashed out on a stainless steel 40bar check valve but it didn't seal properly so I replaced the plastic piston for a brass and rubber one which works ok.
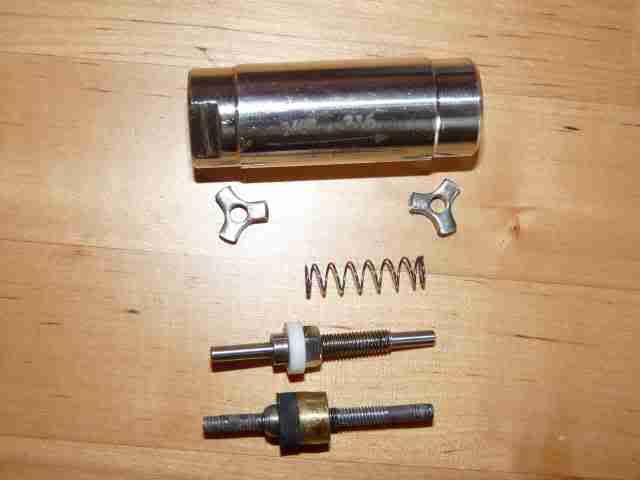
(original piston on top, rebuilt piston below)
To reduce the dead space in front of the check valve there is a bolt projecting from the front of the 15mm piston which fills the fitting to the base of the elbow, I could have mounted the check valve directly to the cylinder but wanted to keep both cylinders the same length.
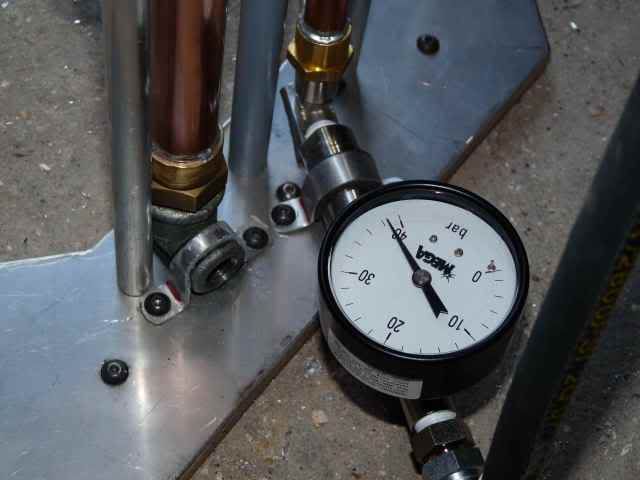
Questions welcome.