soldering metals other than copper
i just made a "pen" gun, the reason i have quotation marks around pen is because it is 16" long, but the piston valve is very similar to a lot of pen guns. everything is epoxyed together. and the reason i posted this here is because i do have a question. i know that copper pipes can be soldered together, but i want to make a small cannon without epoxy, so that it will look nicer and be more durable. can i solder brass tubing to an aluminum spacer, and that spacer to copper pipe? does soldering pipes only work with copper? to those who reply, thank you for lending your experience and knowledge. :thumbup:
qwert123 wrote:well, i was unable to find 1/2" brass tubing in my area, I'm sure i could make a copper spacer if i found the right pipe, could i solder/braze brass to copper? or does it have to be the same metal?
thats a good question,, i dont see why not
i know you can braze copper and braze brass, but togethger idk
- Labtecpower
- Sergeant 3
- Posts: 1297
- Joined: Sat Feb 20, 2010 6:38 am
- Location: Pyongyang
- Has thanked: 5 times
- Been thanked: 13 times
When soldering the metals don't melt, as long as the metal can be wetted by the solder there should be no problems.
- mobile chernobyl
- Corporal 3
- Posts: 756
- Joined: Sun Dec 03, 2006 11:53 am
- Been thanked: 7 times
I've brazed copper with brass. You're getting close to the melting point of copper by the time the brazing rods start to flow so you need to be very careful with flame placement.
Bronze based brazing rods melt around 1500-1600*F where copper should melt somewhere around 1950*C - but there's so many alloys that you can't be exactly sure.
Silver solder is a more common material to use for brazing copper together.
Bronze based brazing rods melt around 1500-1600*F where copper should melt somewhere around 1950*C - but there's so many alloys that you can't be exactly sure.
Silver solder is a more common material to use for brazing copper together.
- Technician1002
- Captain
- Posts: 5189
- Joined: Sat Apr 04, 2009 11:10 am
Silver solder comes in two major varieties.
Silver bearing solder comes on a roll and has a relatively lwo melting point and can be used with a propane torch.
Silver Brazing solder comes in rods and requires a welding torch to use properly.
Silver bearing plumbing solder on the left. Silver brazing solder on the right. Electrical lead - tin in the middle.


Silver bearing solder comes on a roll and has a relatively lwo melting point and can be used with a propane torch.
Silver Brazing solder comes in rods and requires a welding torch to use properly.
Silver bearing plumbing solder on the left. Silver brazing solder on the right. Electrical lead - tin in the middle.


- Fnord
- First Sergeant 2
- Posts: 2239
- Joined: Tue Feb 13, 2007 9:20 pm
- Location: Pripyat
- Been thanked: 1 time
- Contact:
Copper, brass, bronze, tin, steel, stainless, zinc and a few others can be soldered reasonably well. Some stainless grades are harder to solder than others.
Try to avoid aluminum. You'll need special solder and probably an acid based flux. It's possible to solder to aluminum with normal soft solder but it needs to be brought very close to its melting point, and is almost impossible to control.
Try to avoid aluminum. You'll need special solder and probably an acid based flux. It's possible to solder to aluminum with normal soft solder but it needs to be brought very close to its melting point, and is almost impossible to control.
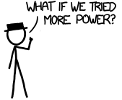
Technician1002 wrote:Silver solder comes in two major varieties.
Silver bearing solder comes on a roll and has a relatively lwo melting point and can be used with a propane torch.
Silver Brazing solder comes in rods and requires a welding torch to use properly.
Silver bearing plumbing solder on the left. Silver brazing solder on the right. Electrical lead - tin in the middle.
(Silver Brazing solder comes in rods and requires a welding torch to use properly. ) To braze you can use a basic torch from homedepot but it will take longer to heat up , in school we use torches that hook up off of the propane tanks from the grill
and another good thing is brazing can be used for higher pressures,
- Technician1002
- Captain
- Posts: 5189
- Joined: Sat Apr 04, 2009 11:10 am
Soft solder is used for water plumbing in the pressure range of 30-150 PSI. 250 is getting very marginal for a joint blowout with soft soft solder. Over 200 PSI should use brazed joints. Hard silver solder is the industry standard for refrigeration work.
Interesting. I remember seeing a post on here that said that a typical solder joint would be rated to about 3000 PSI, including safety factor.Technician1002 wrote:Soft solder is used for water plumbing in the pressure range of 30-150 PSI. 250 is getting very marginal for a joint blowout with soft soft solder. Over 200 PSI should use brazed joints. Hard silver solder is the industry standard for refrigeration work.
POLAND_SPUD wrote:even if there was no link I'd know it's a bot because of female name
- Fnord
- First Sergeant 2
- Posts: 2239
- Joined: Tue Feb 13, 2007 9:20 pm
- Location: Pripyat
- Been thanked: 1 time
- Contact:
I wouldn't trust one to 3,000, but a shear strength calculation using the yield strength of the solder and the joint contact area should give a reasonably accurate number. I've used half inch fittings at 900 psi with no trouble. I wouldn't go much higher though.
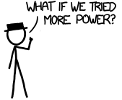
- Technician1002
- Captain
- Posts: 5189
- Joined: Sat Apr 04, 2009 11:10 am
Soft solder being malleable fatigues. Loose solder joints in electronics is a common failure mode where thermal cycles or mechanical vibration cracks the solder joints. Ever had an old TV that cut out and could be fixed by a slap on the side?
In electrical work this is what that failure mode looks like. The fix is to re-solder it. In high pressure pipe a failure is a blowout. Mechanical stress will cause this. It may hold at first, but with time expect a failure with soft solder. This is the reason refrigeration does NOT use soft solder. Mechanical vibration and thermal cycles will cause failures.
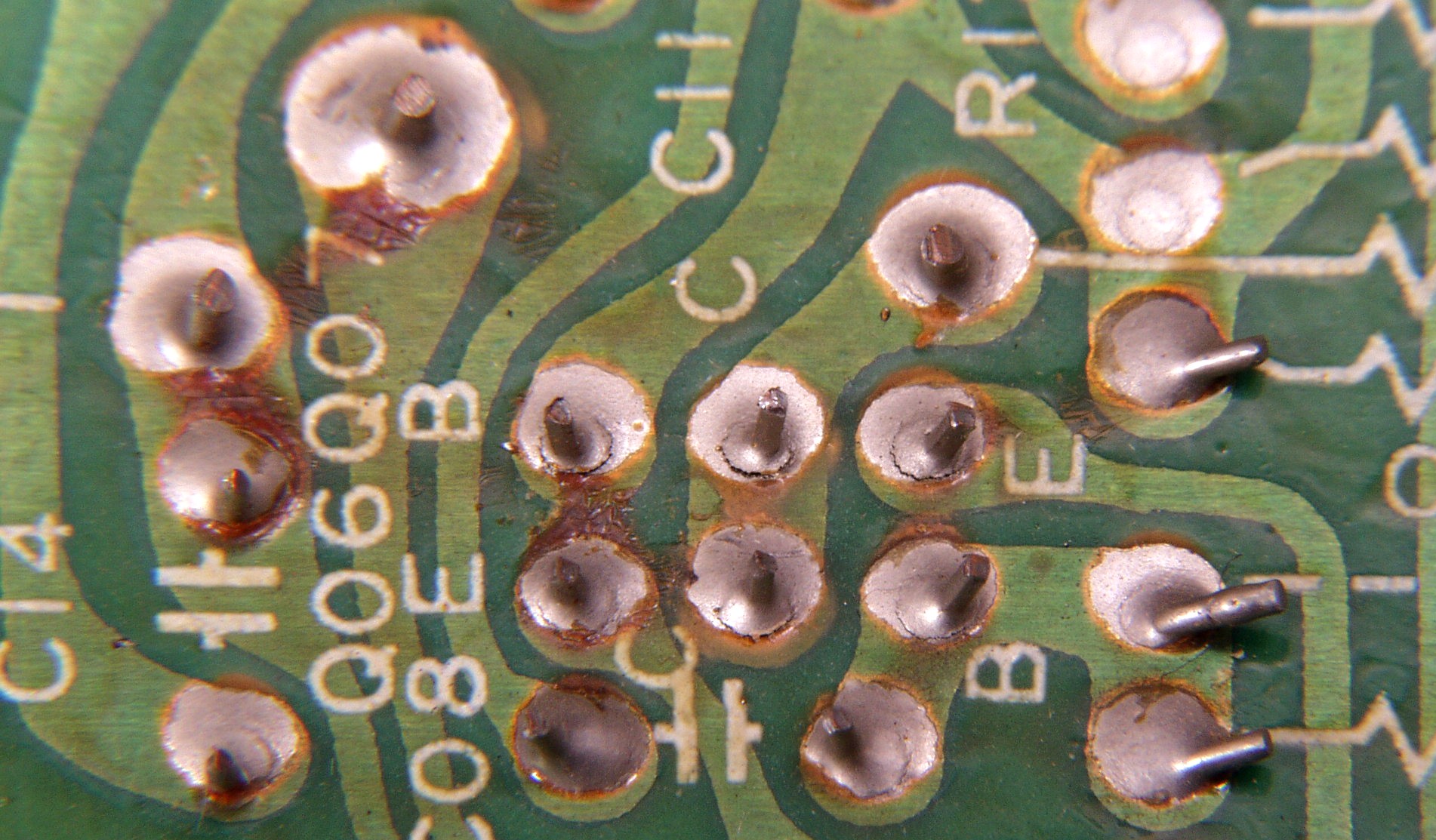
In electrical work this is what that failure mode looks like. The fix is to re-solder it. In high pressure pipe a failure is a blowout. Mechanical stress will cause this. It may hold at first, but with time expect a failure with soft solder. This is the reason refrigeration does NOT use soft solder. Mechanical vibration and thermal cycles will cause failures.
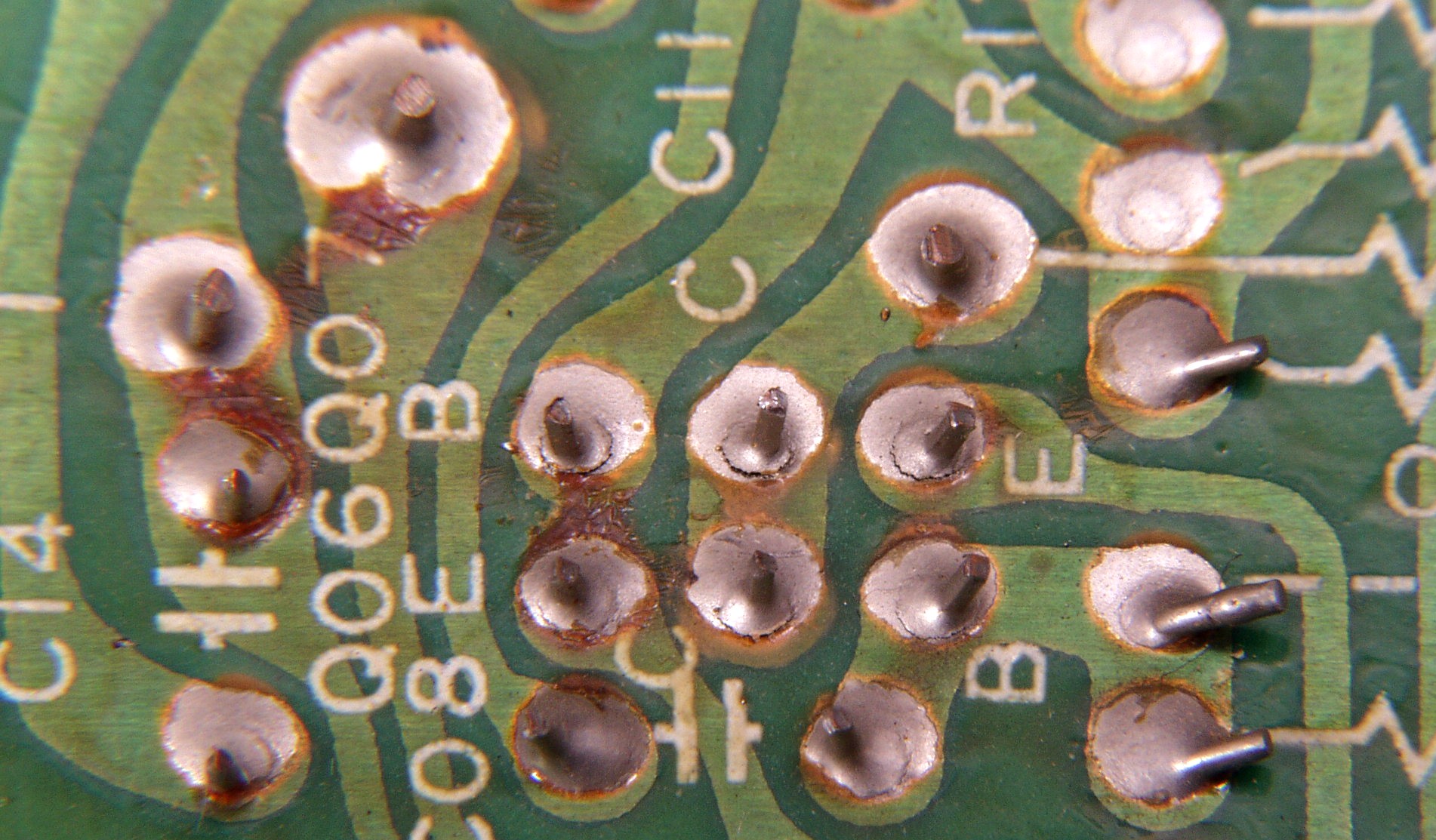